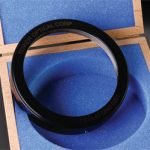
Transmission Flats for Precision Optics: What They Are and How They Work
Wednesday, 11 June, 2025
Zero-Order vs Multi-Order Waveplates: What’s the Difference?
Sunday, 29 June, 2025Introduction
In the world of precision optics, controlling the polarization state of light is critical for a wide range of applications, from laser systems and imaging to quantum optics and telecommunications. One of the most essential tools for achieving this control is the waveplate, also known as a retarder. These finely engineered optical components can modify the polarization state of light without altering its intensity or wavelength, making them indispensable in scientific, industrial, and defense systems.
At Tower Optical, we manufacture high-performance waveplates that meet the tightest tolerances in optical engineering. In this article, we’ll explain what waveplates are, how they work, and why coatings are just as important as the substrate itself.
What Is a Waveplate?
A waveplate is a birefringent optical device designed to alter the polarization state of transmitted light. It does so by introducing a phase shift between the orthogonal components of the electric field of light passing through it. The amount of phase shift is determined by the optical path difference created due to birefringence—a property of certain materials like quartz and magnesium fluoride, where the refractive index depends on the polarization direction of the light.
The phase delay is typically expressed in degrees or wavelengths:
-
Quarter-wave plate (λ/4) introduces a 90° phase shift
-
Half-wave plate (λ/2) introduces a 180° phase shift
-
Full-wave plate (λ) returns the polarization to its original state
These waveplates are specifically cut and polished to thicknesses that achieve the desired retardation at specific wavelengths.
How Do Waveplates Work?
Waveplates operate based on birefringence. When linearly polarized light enters a birefringent material, it splits into two orthogonal polarization components:
-
Ordinary ray (o-ray), which experiences one refractive index
-
Extraordinary ray (e-ray), which experiences another
Because of the difference in refractive indices, the two rays travel at different speeds and acquire a relative phase shift. Upon exiting the waveplate, these rays recombine, and their phase relationship results in a new polarization state.
For example:
-
A λ/4 waveplate can convert linearly polarized light into circularly polarized light, and vice versa.
-
A λ/2 waveplate can rotate the plane of linear polarization to any desired angle.
Types of Waveplates
1. Zero-Order Waveplates
These are constructed to have a retardation of exactly λ/2 or λ/4 at the design wavelength, offering superior temperature and wavelength stability.
2. Multiple-Order Waveplates
Thicker than zero-order plates, they achieve the desired retardation through several full-wave cycles. They are more sensitive to wavelength and temperature shifts but are often more economical.
3. Achromatic Waveplates
Made from two different birefringent materials, achromatic waveplates provide consistent retardation over a broad wavelength range—ideal for broadband sources like white light or tunable lasers.
Applications of Waveplates
Waveplates are used in numerous optical systems that require precise polarization control, including:
-
Laser beam shaping and modulation
-
Optical isolators and circulators
-
Polarimeters and ellipsometers
-
Spectroscopy
-
Quantum computing setups
-
Fiber optics systems
They also play a vital role in research environments, aerospace systems, and optical instrumentation.
Why Optical Coatings Matter
A waveplate is only as effective as its surface coatings. Proper coatings are essential to ensure high transmission, minimal reflection, and durability. Here’s why they matter:
1. Antireflection (AR) Coatings
Waveplates are typically coated with broadband or narrowband AR coatings to minimize reflection losses at the entrance and exit surfaces. Without these coatings, reflections can reduce transmitted power and introduce ghost signals or unwanted interference in sensitive optical systems.
2. Enhanced Damage Threshold
For high-power laser applications, coatings need to have a high laser damage threshold (LDT) to prevent degradation or failure under intense beams. At Tower Optical, we provide coatings that are rigorously tested to withstand specified LDTs based on customer requirements.
3. Environmental Protection
Coatings can also provide protection against humidity, scratches, and chemical exposure, extending the operational life of the waveplate in harsh environments.
4. Polarization Purity
Uncoated or poorly coated surfaces can introduce unwanted birefringence or depolarization. Precision coatings help maintain the polarization integrity critical for interference-based systems and polarimetric analysis.
Material Considerations
Waveplates are usually made from materials with high birefringence and excellent optical clarity. Common materials include:
-
Crystal Quartz – widely used due to its durability and stable birefringence
-
Magnesium Fluoride (MgF₂) – excellent for UV applications
-
Polymer films – used for low-cost, low-precision applications
At Tower Optical, our waveplates are made from optically pure crystalline materials with flatness and parallelism tolerances appropriate for the intended wavelength and application.
Quality Control and Tolerances
Precision waveplates require:
-
Surface flatness typically better than λ/10 at 632.8 nm
-
Retardation accuracy of ±λ/300 or better for high-end systems
-
Parallelism better than 10 arc seconds
-
Scratch-dig surface quality of 10-5 or 20-10 per MIL-PRF-13830B
Every waveplate we produce is inspected and tested with interferometry and polarization analysis to ensure compliance with stringent optical standards.
Final Thoughts
Waveplates are not merely optical accessories—they are precision tools that enable sophisticated control of light. From rotating polarization states to enabling complex optical measurements, their role is foundational in modern optics. At Tower Optical, we understand the critical importance of both the substrate and the coatings, which is why our waveplates are engineered and tested to meet the most demanding optical performance requirements.
Explore Waveplates by Tower Optical
Tower Optical Co., Inc. offers a full line of custom and standard waveplates, including zero-order, multiple-order, and achromatic types. We provide precision coatings for UV, visible, and IR applications tailored to your specific system requirements.
To learn more or to request a custom quote, visit https://www.toweroptical.com or contact our technical team today.
Sources:
-
Hecht, E. Optics, 5th Edition. Addison-Wesley.
-
Malacara, D. Optical Shop Testing, Wiley.
-
Tower Optical Co., Inc. internal manufacturing specifications and coating protocols
-
National Institute of Standards and Technology (NIST) – Optical Metrology Standards