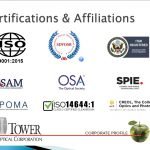
The Impact of Photonics on the World
Tuesday, 7 July, 2020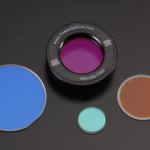
Waveplates Explained and Factors To Consider
Monday, 27 July, 2020How They’re Made: A Guide To Precision Optical Lenses
Precision optical lenses come in many shapes, sizes, and materials and perform various functions. Myriad lens types are made for catalog stock or to unique customer requirements. Each side may be flat, convex, or concave, and the curves may be shallow or steep. Their outer rim, most often cylindrical, may be any other shape to fit the package or the function. And the materials from which they’re made include crystals, plastics, and hundreds of specialty glass types.Applications for precision optical lenses are found in the fields of defense, mapping, security, medicine, industry, the sciences, and more.
Precision optical lenses are used alone or in combination with other optics to focus, diverge, or collimate light, or to correct image aberrations originating elsewhere. Whether your industry applications require standard, cylindrical, ball and drum, or mini lenses, Tower Optical can meet your most demanding specifications.
Selecting and Sourcing the Material
The first step in lens fabrication is choosing the right material. Whether chosen by the customer or fabricator, the factors include its chemical and environmental durability, spectral range of transparency, refractive index (the degree to which it bends light), refractive index homogeneity, laser damage threshold, workability, and cost. A popular choice is high purity fused silica, chosen for its broad spectral
range of transparency, its light weight, its chemical resistance, hardness, toughness, and durability, and its extreme resistance to thermal shock. Another popular choice is known as NBK-7, a proprietary borosilicate glass type that shares the advantages of fused silica to a lesser degree, at a much lower price point, while taking less work to shape and polish. Both of them have a low index of refraction. There are hundreds of glass types, plus crystalline materials including silicon, germanium, calcium fluoride, and magnesium fluoride, filling every niche.
Planning
Before starting fabrication, a production plan is written and sent with the blanks to the shop. This plan specifies the order of operations, the interim target tolerances, the particular machines, fixtures, methods, and materials to use. This plan will vary depending on the configuration and tolerances of the lenses, the quantity to be produced, and the working properties of the lens material. Some lens surfaces must be worked individually while others can be worked together on what is called a “block.” The production planner is intimately familiar with the shop capabilities and typically experienced in operating all the machinery. Efficiency, price, and quality all start with planning.
While the machinery chosen and the order of operations may vary, they generally group into the following categories:
Blocking
Where geometry allows, multiple lenses can be affixed to a backing plate so that they are all held in strict relationship to each other. In this way a single machine operation can work 5 to 100 or more parts in nearly the same time as one. And just as a stool is more stable with three legs than one, precision can be improved as well.
Rough-shaping Lens Features
To prepare the blanks for finishing operations, they must be sculpted to approach their final dimensions and shape. The total thickness is machined down, the edges brought to slightly over final dimension, and the curves are scooped out. All this is done with high-speed rotating diamond-impregnated tools
mounted on several configurations of stiff machine bases. Dicing, core-drilling, milling, and curvegenerating are collectively known as “shaping.”
Lapping
Any tool marks left from shaping are removed, the surface is smoothed to a satin sheen, and final dimensions are approached within tens of microns by lapping operations. In some cases this is done on the same machines as in rough-shaping, using finer diamonds and slower feed rates. In other cases, a slurry of fine abrasive grit suspended in water is rubbed between the lens’ surface and a lapping tool of the complementary shape (concave tool for a convex surface, etc.) When lapping is complete, the lenses are ready to take a polish.
Polishing
The sheen is refined to a water-smooth surface by microscopic removal of the irregularities left from lapping. Only 10-20 m is removed in total. Several technologies are used to polish lenses. Some are over a century old and still produce among the best surfaces; others are being developed even now.
Almost all of the methods depend upon cerium oxide in a water-based slurry to do the work on glass, and microscopic diamond, alumina, or other minerals to do the work on crystals. The shape of the polished surface is refined to match the mathematical ideal during polishing to tolerances measured in nanometers.
Centering and Edging
The two curves on the lens’ opposing faces must be aligned to the center of the lens so that there is no wedge between them. This alignment is called Centering, and the Edging part is because it is frequently done after both sides are polished: The polished lens is optically aligned to the centering machine, and its edge is lapped concentric to its optical axis. Where this operation is required is the one exception to the statement that shaping approaches final dimensions – the lens edge is left 1-2 mm over final diameter throughout fabrication, and finally the lens is edged down to a centered condition.
Coating
To reduce light losses due to reflections, an anti-reflection coating is deposited on the finished lenses. Unlike the dip-coating typical in eyeglass lenses, these coatings are built up of alternating microscopic layers of refractory materials according to a computer-designed recipe, in a vacuum chamber.
Inspection
Tolerances are verified throughout the entire fabrication journey using a variety of mechanical and optical methods. While inspection never adds quality, it ensures final quality while reducing costs. A proper inspection regimen is key to a successful product.
Tower Optical, Your Supplier of Choice
Tower Optical has been providing lenses to the precision optics community for decades. Tower Optical maintains long-term relationships with skilled and experienced personnel to cover all stages of lens production from sales engineering to final inspection. Tower is ITAR compliant and ISO certified. Contact Tower Optical for your every precision optics need.