
Overview of Waveplates
Friday, 23 December, 2016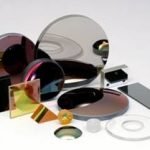
What Makes a Good Precision Optics Company?
Friday, 23 December, 2016The wave plate (sometimes written as waveplate or wave-plate and also known as a retarder) transforms one state of polarization into another. Variants of this simple optical device perform multiple functions that are useful in countless applications.
The wave-plate consists of one or two precisely oriented plane-parallel plates of crystal quartz (SiO2), magnesium fluoride (MgF2), and sometimes sapphire (Al2O3).
The two most simpleretarders are quarter wave and half wave retardance. The quarter-wave plate transforms between linear and circular polarizations. The half-wave plate can rotate the azimuthal orientation of linear polarization, or switch between right-circular polarization and left-circular polarization, and more. Other retardation values are available from some manufacturers who specialize in custom waveplates. A single plate usually has a value ofsome odd multiple of quarter or half wave retardance such as 5 ¼ waves or 13/2 waves; these are called “multiple order waveplates.”
With skilled design and precise manufacturing, a single plate can perform various functions at two different design wavelengths. If you want some combination of ¼, ½, or null effect at two different wavelengths, ask your wave-plate supplier specialist– you may be surprised to find how much is possible!
Two plates of the same material can be assembled so that their difference is only ¼ wave or ½ wave; these are called compoundzero-order wave plates. While a bit more expensive than multiple order, they are much less sensitive to temperature or wavelength variations.
Achromatic wave-plates,that offer essentially constant retardation across a broad band, consist of two plates of different materials. Typical bands are 465-610 nm, 610-850 nm, 700-1000 nm, and 1200-1650 nm. They offer the flattest spectral response.
Retarders of all types are available either unmounted or in cell-mounts. The cell-mount, a ring of anodized aluminum with orientation marks and identifying information, is made to fit into standard optical hardware and protects the plates from chips or distortion. If the retarder consists of two plates, they may be cemented together, optically contacted, or be air spacedwith a thin stainless steel ring leaving an air gap between the plates. Of these constructions, the air-space offers the greatest power handling, greatest laser damage threshold, and greatest thermal range.
Because of the specialized nature of wave plate design and metrology and the extreme precision of fabrication required, few optical manufacturers offer waveplates – and fewer still can meet all your needs consistently. Choose your supplier carefully with these thoughts in mind:
Do they understand your needs? Can you communicate with them well? Do they specialize in wave-plates? Do they offer design services? Do they have all the required state of the art metrology, including phase-shift interferometers, autocollimators, microscopic visual inspection, polarization alignment, extinction measurement, and in-house optical retardation instrumentation? Can they meet specifications such as 0.5 arc-second parallelism, 10/5 surface quality, ±l/200 retardation @632.8 nm, and l/10 transmitted wavefront? Can they verify all these parameters with an ISO-certified quality system? Have they been in business for awhile and do they have a good reputation?